Get the most out of your ticket data with labelling
20 June 2023
Do you often have to deal with error messages and malfunctions? Analysing all these tickets involves huge amounts of extra work. But that data is also a valuable source of information. So how can you get use that information to your advantage? Add labels to your ticket data! This gives you an insight into all kinds of problems.
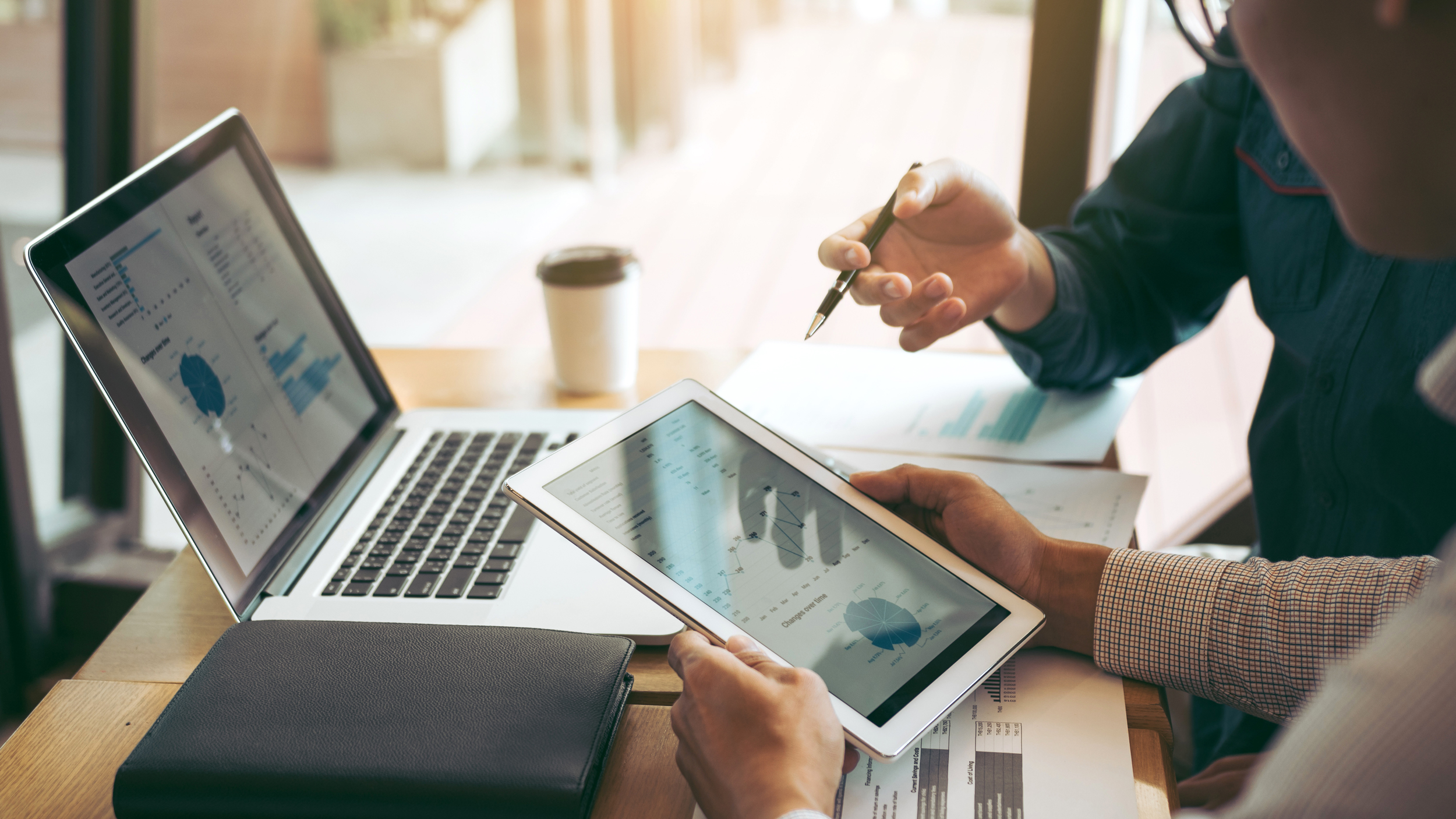
From data to information
Labelling is all about enriching the data by adding information. For example: A field service organisation responsible for telecom street cabinets asked us for help. They received 7,000 malfunction tickets throughout 2021 for 13,000 street cabinets. They didn’t have any information about the performance of the individual assets.
The time and location of the malfunctions were known for the tickets, but the cause wasn’t specified. In this case, one of the problems was the hotter temperature, especially in the summer months. By adding temperature as a label to the existing data, we were able to make comparisons with previous years. This is how you add information and therefore value to the data.
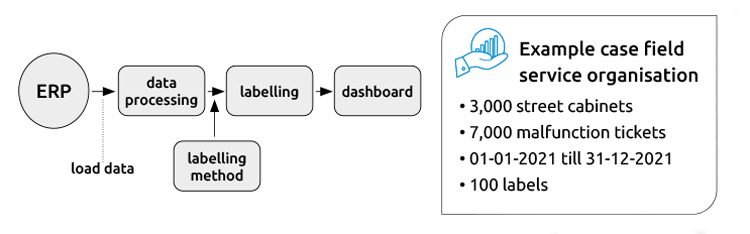
Here it is important to make a distinction between relative and content labelling. With relative labelling, you look at the location, date and time. You can determine the following, for example: if there is less than 30 days between two tickets, we’ll call it a repeat malfunction. You determine this on the basis of a possible SLA or business logic. Content labelling is about the reason for a ticket, such as a temperature alarm or the loss of a connection.
From information to logic
When applying labels, validity and logic are the most important things. You guarantee validity by assigning the labels correctly. When doing this, work together with the experts – in this case the planners, who assess, allocate and schedule the tickets. This immediately raises awareness among the experts. If you find out how these experts assess tickets and on which basis they make decisions, you can systematically record that knowledge. This creates logic that you can repeat with future tickets.
To label tickets, you can, for example, link the database of your ERP system to a reference table and thus establish the logic, but this is very limited and requires many actions. That is why we use the Microsoft Azure platform. With various components from Azure you create a so-called data street, which makes automation possible.
Processing ticket data in Microsoft Azure
- unstructured storage in Azure Blob Storage
- multi-step processing using Azure Databricks
- stored as parquet files in the Azure Delta Lake
From logic to value
The data has now been processed, structured and enriched. But what you want is insight into that data. We use the Power BI visualisation tool for this. You can easily connect this to the stored data in the Blob Storage through the Azure platform. The data is then refreshed daily and loaded into the dashboard. This is dynamic and interactive, which means you can make cross-sections and analyses of the data as you see fit.

By also adding external data sources, you take the analyzes to an even higher level. In our example, we used data from the National Weather Service to also include the ambient temperature of each location. Then, for example, you can plot it in a graph on a time scale in order to recognise trends and compare different periods.
What does it yield?
On the dashboard, the field service organisation can now see at a glance which locations have the most malfunctions, how many repeat malfunctions there are and which types of malfunctions they involve. Without proper labelling, these types of trends are rarely detected.
So deploy the vigilance and expertise of a planner or technician for good labelling and use dashboards to make all the malfunctions transparent with a single click. You establish relationships between labels and the time of registration. This way, you can see how a location is performing, for example, in warm weather. You can solve any problems and set up and refine the related processes.
Ultimately, this results in more uptime for your assets. The starting point for improvement and prevention!
- Repeat malfunctions: insight into recurring problems with specific assets
- Trends: insight into common malfunctions within a certain period
- Maintenance effectiveness: determining the most effective form of maintenance for each type of malfunction
Contact us for a non-binding scan
Do you want to know how you can get more value from your ticket and asset data? Then make an appointment for a non-binding scan. Together we can take the first step towards achieving added value for your organisation and assets.
Contact?
Jasper Habermehl
Manager Data & IoT